An electric motor uses the attraction
and repulsion of electromagnets and permanent magnets to produce rotary
motion. The following is a diagram of a permanent magnet DC motor. It
works by sending a current through a coil of wire, making that coil an
electromagnet. That coil will then be attracted or repelled by
permanent magnets. The coil is on an axle so that it will rotate. The
magnetic forces will cause it to rotate one way or the other, depending
on the polarity of the applied voltage.
A permanent magnet DC motor |
The rotating part of the motor, that includes the armature and
commutator is called the rotor. The armature is the rotating coil. The
commutator is a split ring that rotates with the armature. The
stationary part, including the field magnets, brushes and housing is
called the stator.
The rotor from a simple permanent magnet DC motor. You can see the split in the commutator on the left side of the shaft. |
The brushes, often made of carbon, contact the commutator to provide power to the armature.
The field magnets are the permanent magnets or electromagnets that provide a magnetic field for the armature to interact with.
As the commutator rotates the brushes stay in contact with it
continuing to supply power. The commutator also acts as a switch. With
each half-turn of the armature, the commutator changes which direction
the current flows through the coil. During one half-turn the armature
is magnetized in one direction and during the other half-turn it is
magnetized in the other. When the armature lines up with the field
magnets the commutator reverses the polarity of the armature so that
the magnetic fields push then pull the armature another half turn to
line them up again. This repeats over and over as the motor turns.
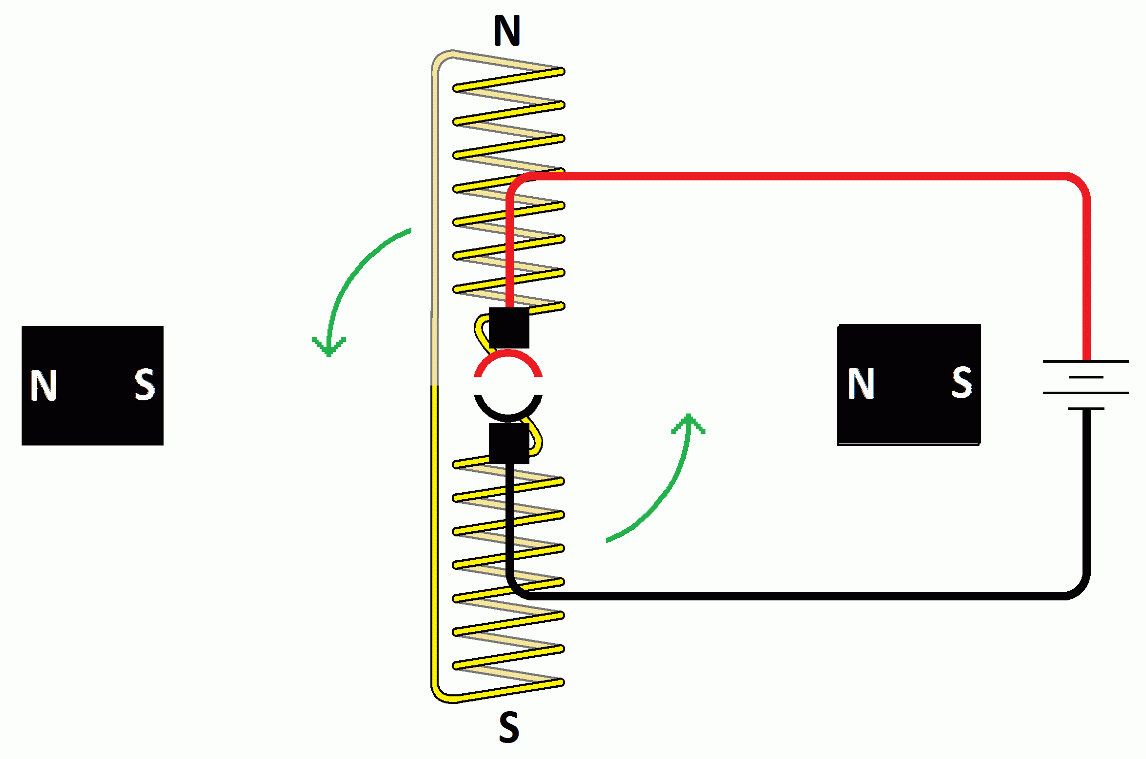
|
|
The current through the armature causes the magnetic field to be
oriented as shown. The north pole of the armature is attracted to the
south pole of the left magnet. Likewise, the south pole of the armature
is attracted to the north pole or the right magnet.
|
|
|
|
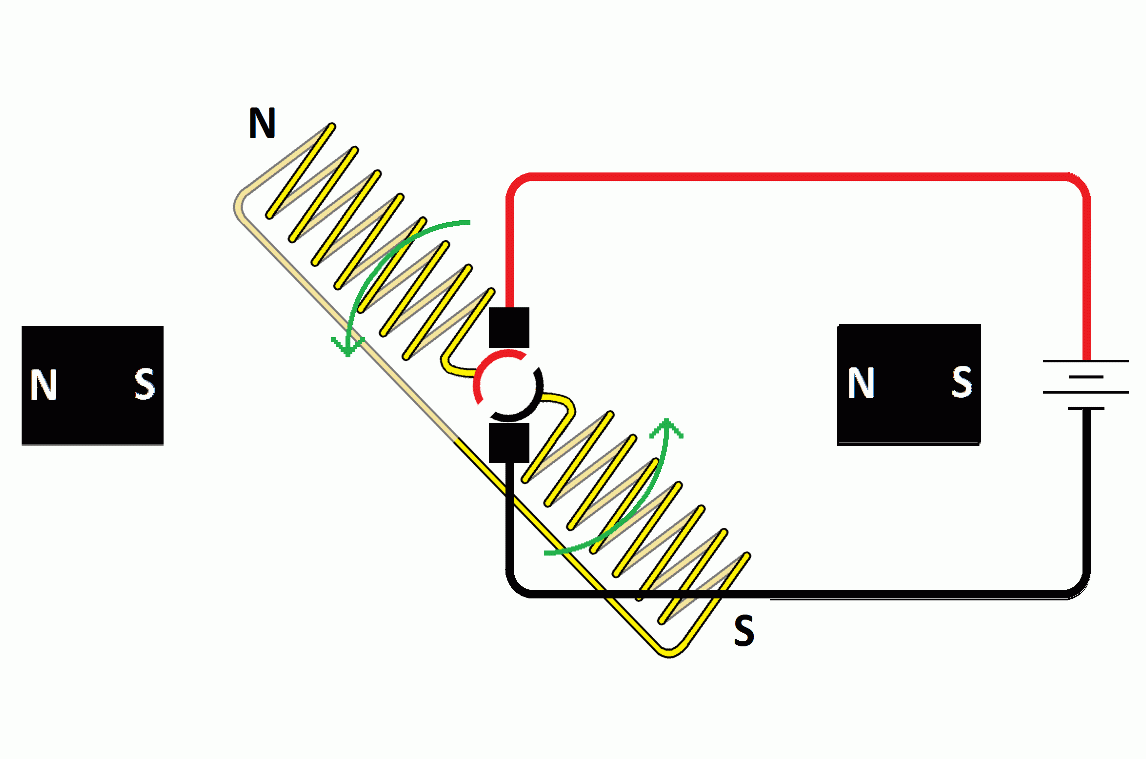
|
|
This magnetic interaction causes the armature to rotate counter
clockwise. The poles of the armature try to line up with the poles of
the field magnets. |
|
|
|
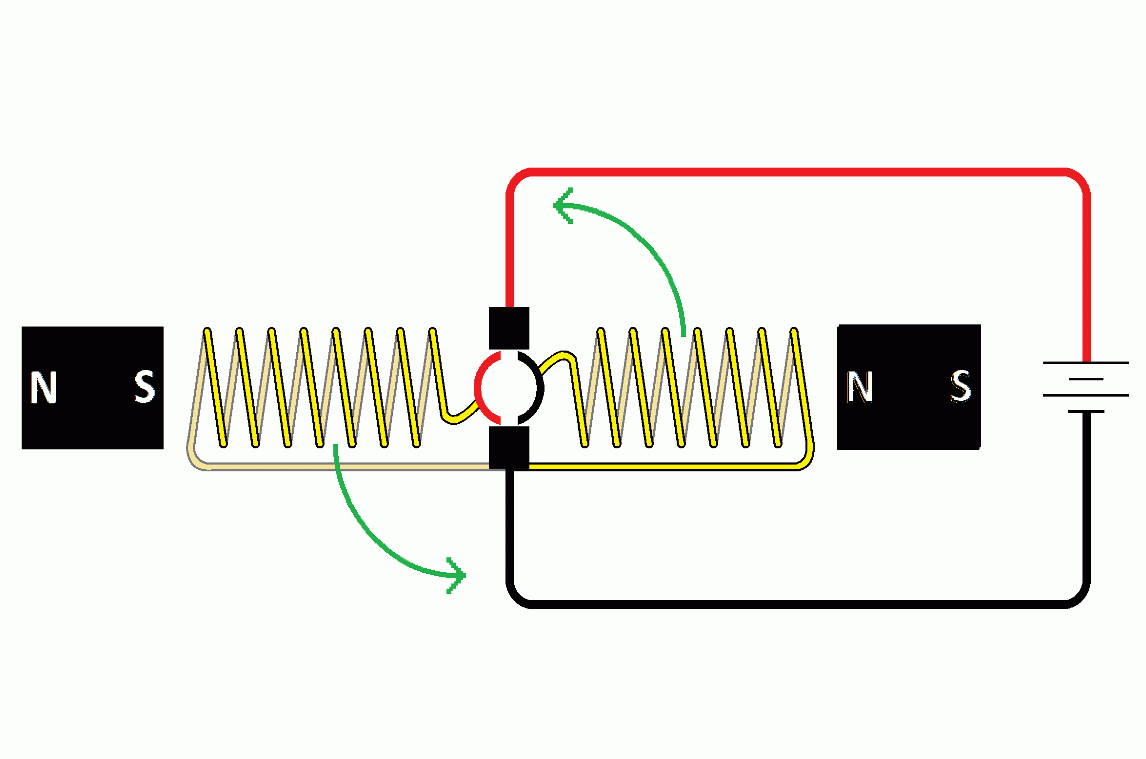
|
|
Momentum carries the armature past the magnets as the commutator swaps the battery connection. |
|
|
|
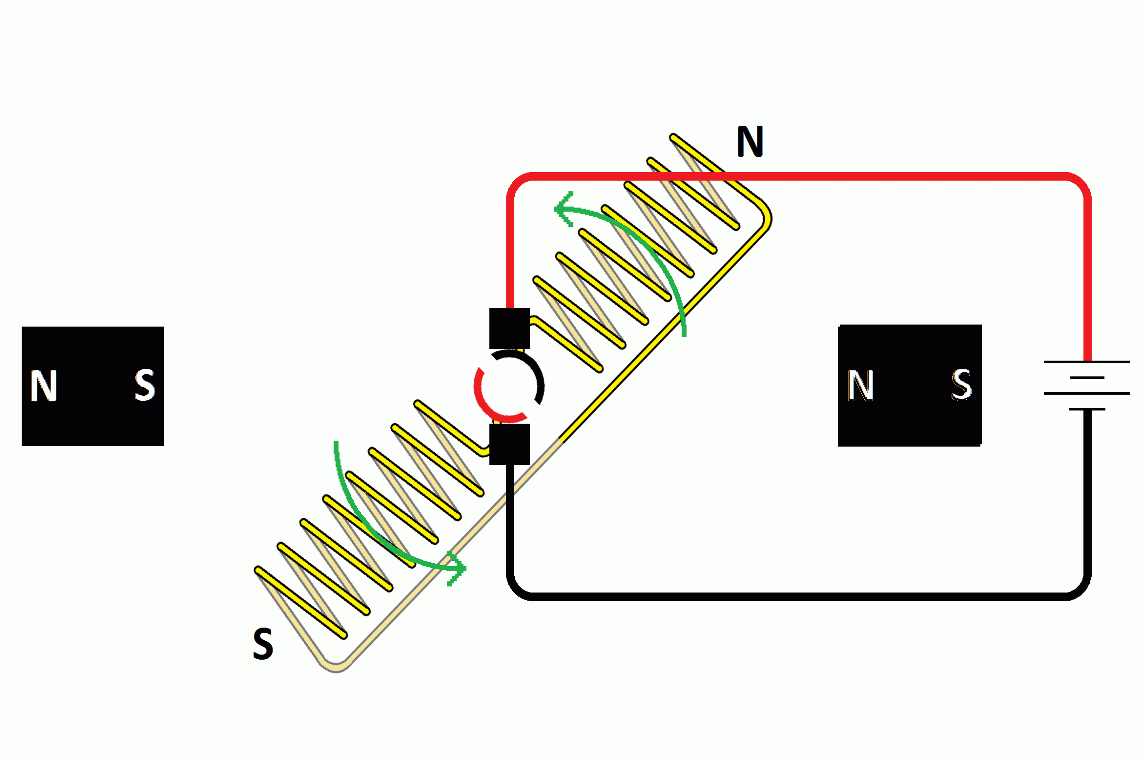
|
|
The commutator has switched the poles of the armature. Now the north
pole of the armature is repelled from the north pole of the right
magnet and vice versa. The armature continues to rotate. |
|
|
|
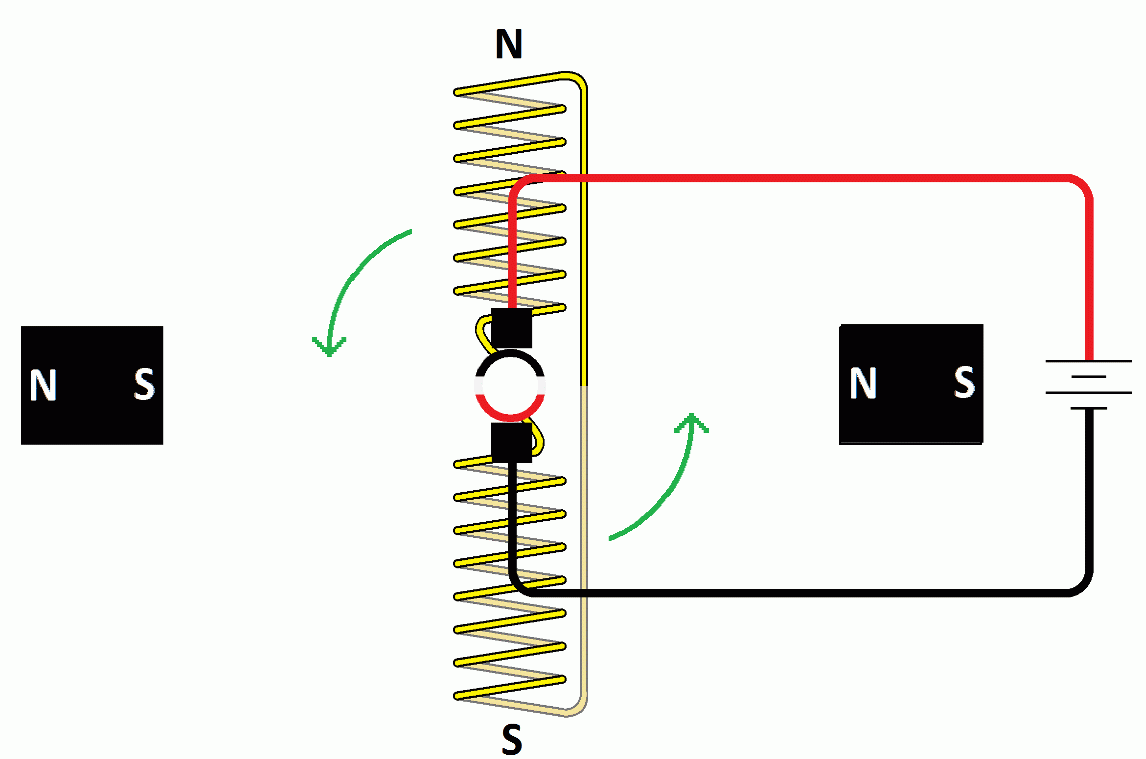
|
|
Now the armature has made ½ turn. The former north pole is now the
south pole and vice versa. The next half cycle begins like the first. |
|
|
|
How do you know which end of the armature will be north and which will
be south. Make a fist with your right hand with the thumb pointing out.
Your fingers curl in the direction of conventional current and you
thumb points to the north pole. This is called the right hand rule. For
electron flow use your left hand.
Generators
A DC generator is exactly the same as a DC motor. If you spin the
armature of a DC motor it will produce DC voltage (and current if there
is a circuit between the terminals). You can demonstrate this by
putting a voltmeter or current meter across a motor and spinning the
armature. You may even get enough current to run a small light bulb or
LED. Before nuclear submarines, many diesel submarines used motors to
run the propellers from batteries when submerged. When surfaced, diesel
engines turned the propellers. Since the electric motors were on the
propeller shafts they were also turned by the engines. Therefore, while
surfaced the motors were used as generators to charge the batteries.
1
Often electric vehicles use the traction motors (the motors that turn
the wheels of the vehicle) as generators. While braking they put some
charge back into the battery.
If you short the terminals on a motor the motor will self-brake. This
is because turning the armature generates current. This current creates
a magnetic field that tries to turn the motor in the opposite direction
to which it is rotating. You can demonstrate this by spinning the
armature of a small electric motor. It should spin freely. Next use a
clip lead to short the terminals together and spin the armature again.
You will see that the armature quickly stops. Electric trains, from
light rail to heavy diesel-electric locomotives often use this effect
to help slow or stop the vehicle. This called dynamic braking.
A slight change in design creates an AC generator or alternator.
Instead of a commutator (a single split slip ring) an alternator has
two complete slip rings with a brush on each. A commutator will cause
the generator to produce DC. It acts as a switch to cause the current
to flow in only one direction.
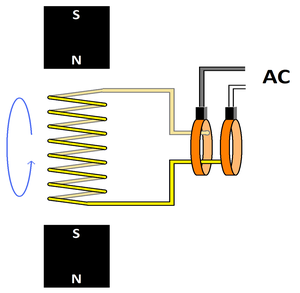
|
A generator with slip rings instead of a commutator produces alternating current and is called an alternator. |
|
|
A commutator causes the generator to produce direct current (this is identical to a DC motor). |
Although this design with slip rings will produce AC, this is not how
working alternators are designed. In typical alternators the
armature is fed DC through the slip rings making the armature an
electromagnet. The armature rotates inside the stator which is
lined with coils. Alternating current is produced in the stator coils
as the armature's magnetic field spins past them. Alternators will be
covered in more detail in the volume on AC circuits.
Here is an interactive
simulation
of an alternator and generator:
Small DC motors are usually made with permanent magnets. Before the
development of rare earth magnets permanent magnets were not powerful
enough for large motors. Large motors are usually made with
electromagnets for the field magnets. The permanent magnets are
replaced with coils of wire called field coils as shown below. There
are two ways to make electromagnet motors: series wound and shunt wound.
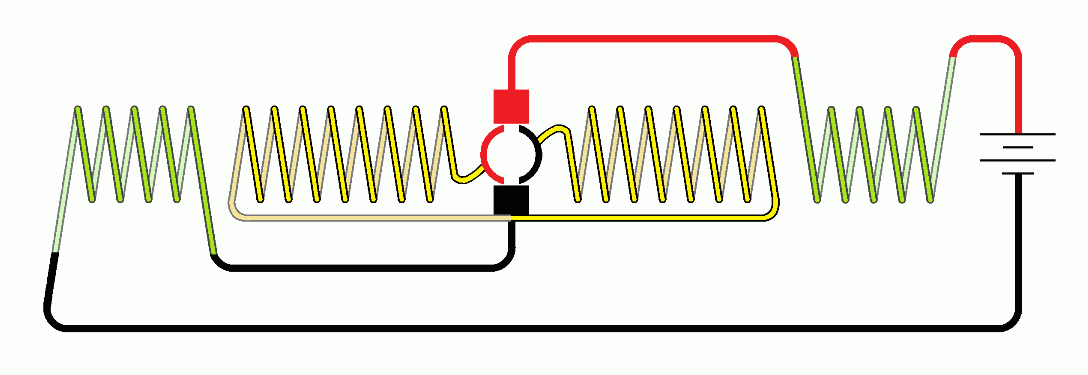
|
Series wound electromagnet DC motor |
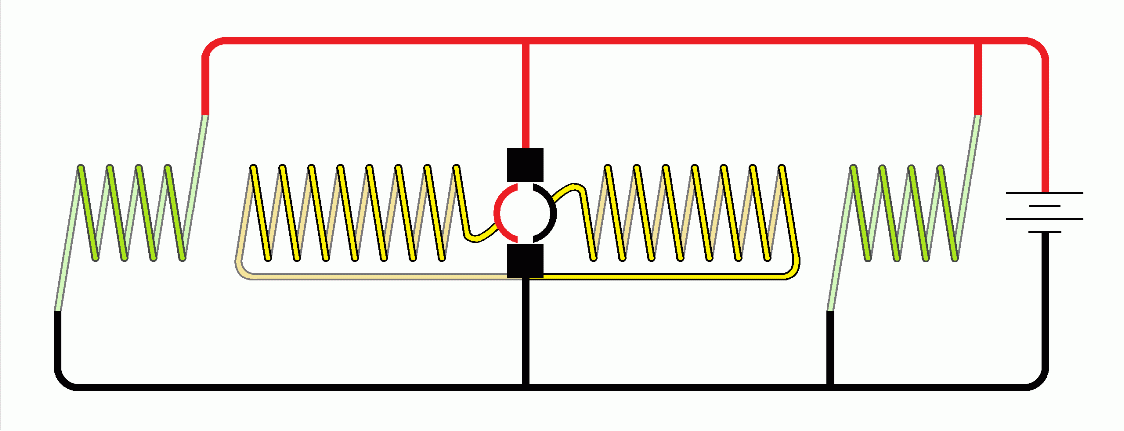 |
Shunt wound electromagnet DC moror |
|
Series wound motors have the field coils connected in series with the
armature. Shunt wound motors have the field coils connected in parallel
with the armature (i.e. a shunt or bypass). A shunt wound motor
typically runs at a fairly constant speed regardless of the load
2 when
operated within its design parameters. This is because the strength of
the magnetic field from the field winding is relatively unaffected by
the current through the armature winding.
As mentioned above, a DC motor is also a generator. When a motor is
spinning it produces current that opposes the current that is driving
the motor. This is called back EMF just as is the the current produced
by self induction. When a motor is slowed by a heavy load it produces
less back EMF. Therefore more current flows into the motor and it
produces more torque. This is a convenient negative feedback system.
When a motor is lightly loaded it needs and has less torque but when
heavily loaded it needs and has more torque. This effect is much more
pronounced in a series wound motor. With the field coils in series with
the armature you get more current in the field coils as well as the
armature when the motor is slowed by a heavy load. A series wound motor
should never be operated with no load. It will turn at such a high
speed that centrifugal force could damage it. For example, a series
motor would not be used to drive a belt because if the belt slips the
motor could spin fast enough to damage itself.
Some small DC motors are made with a two coil armature similar to the
diagrams above. However, they are usually made with three or more coils
in the armature.
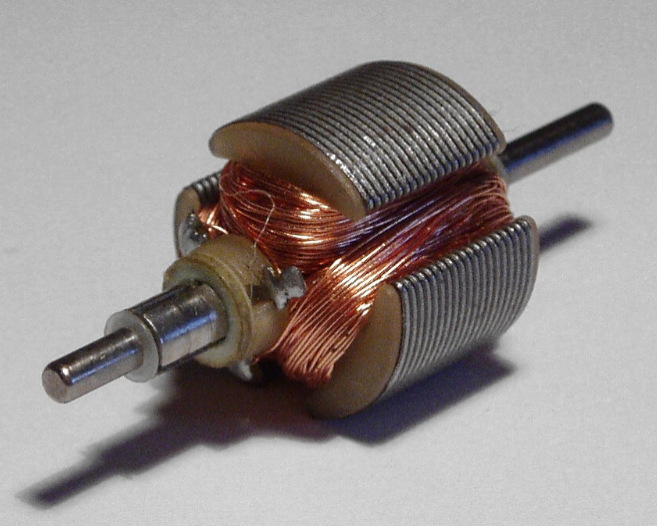
|
A rotor from a permanent magnet DC motor with a three-coil armature.
Like most motors, the armature has a core made of laminated soft iron.
|
|
|
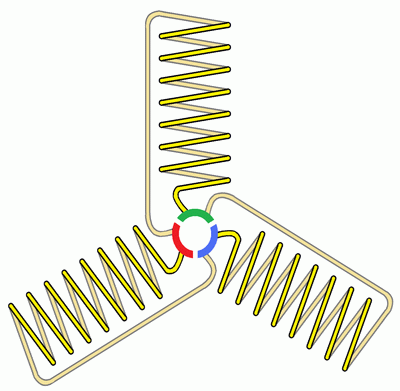 |
Wiring of a three coil armature and commutator.
|
|
Each coil has its own contact on the commutator so most commutators
have more than the two splits shown in the diagrams. Having multiple
coils in the armature increases efficiency. Only the coils near the
field magnets are energized leaving the others dormant while they are
far from the magnets.
1
|
Many submarines were also
designed more like a diesel-electric locomotive. The diesel engines ran
generators that both charged the batteries and ran the motors on the
propeller shafts. On these designs there was no mechanical connection
between the diesel engines and the propellers.
|
2 |
In this case the load is
how much whatever the motor is turning resists that turning force. In
other words, how hard the motor is working.
|